|
Post by jfc on Jul 21, 2008 8:58:13 GMT
Ive just got a quote to repair my Default 625 ( No i didnt smash it up good ! ) ;D It was varying in speed and a little smoke appeared . £140  I'm wondering if it's worth repairing or do i bite the bullet and buy a new router  It's been repaired before and is about five years old .
|
|
|
Post by gazza on Jul 21, 2008 10:56:59 GMT
|
|
|
Post by jfc on Jul 21, 2008 11:03:59 GMT
But that one is reconditioned , it could have had more use than mine 
|
|
|
Post by gazza on Jul 21, 2008 11:14:15 GMT
99.9% of the time they are unused, and have a years guarantee any way. The same model brand new is £199. From the same seller. HTH Gazza.
|
|
|
Post by engineerone on Jul 21, 2008 11:25:48 GMT
no one could have as much use as yours ;D paul 
|
|
|
Post by big-all on Jul 21, 2008 12:23:29 GMT
|
|
|
Post by Keith on Jul 21, 2008 12:47:45 GMT
Get a new one, I had one repaired and they gave it a 3 month warranty. After 3 months and one day it set itself on fire 
|
|
|
Post by big-all on Jul 21, 2008 19:43:45 GMT
surely if they can teach it to set fire to its self it could have fixed its self for a bit longer ;D ;D 
|
|
|
Post by jfc on Jul 26, 2008 6:06:54 GMT
Anyone used the Triton in anger ? Can it handle heavy work for long periods ?
|
|
|
Post by jake on Jul 26, 2008 7:48:59 GMT
I've never had a problem with mine, but it doesn't get heavy trade use. I think most of it is well built (motor and so on I wouldn't be worried about), but I'd be very wary of the rise/fall movement as it's pretty plasticky.
|
|
|
Post by lynx on Jul 26, 2008 8:03:09 GMT
If your used to the 625 i wouldn't opt for the triton. Powerful but clumsy in the rist/fall department when freehand.
|
|
|
Post by jake on Jul 26, 2008 8:08:09 GMT
Oh yes, definitely not for freehand work - it is rubbish that way up.
|
|
|
Post by jfc on Jul 26, 2008 9:32:12 GMT
I only need it for table use . Anyone got a Festool in a table ?
|
|
|
Post by paulchapman on Jul 26, 2008 9:55:21 GMT
|
|
|
Post by jfc on Jul 26, 2008 10:08:15 GMT
Hmmmm was sort of thinking of going away from Default as this is the fith time i have had to put one in for repair and the third 625 i have totally buggered ;D
|
|
|
Post by lynx on Jul 26, 2008 10:49:24 GMT
If it's for the table only, then the triton wins hands down just for the fact you can project the collet above the face of the table for easy cutter changing.
|
|
|
Post by sainty on Jul 26, 2008 11:03:31 GMT
festooool......festool is calling you........................
|
|
|
Post by lynx on Jul 26, 2008 12:47:22 GMT
i think the festool would be a waste under the table. All those to hand features will now be out the way and hard to get too, i maybe wrong here. As Jason asked, anyone have the festool in a table?
|
|
|
Post by sainty on Jul 26, 2008 12:58:26 GMT
|
|
|
Post by engineerone on Jul 26, 2008 15:05:37 GMT
com one this is jason we are talking about ;D the new festo is supposed to be really good for table use though. and i certainly agree about down sizing the dewalt exposure though. for bench only the triton is always coming out the best in tests paul 
|
|
|
Post by Scrit on Jul 26, 2008 18:51:31 GMT
I can think of three completely different approaches. Firstly if you are perpetually destroying DW625s (and I don't know how you do that, either, but then again I don't shove mine in a table all that often) then why not consider buying a really cheap router and sticking that permanently under the table instead, for example the 1300 watt 1/2in beastie currently on offer at my local LiDL for under £30, or you could plump for something a bit better but nonetheless cheap like one of the Performance Pro routers sold by B&Q for well under a ton. You might like to consider hooking up the router tabkle to a cheap vacuum cleaner such as an Earlex as I suspect that you are running without any dust extraction and it's the dust which is knackering the DW625 (as it would also knacker even the "mighty" Festool) Second solution is to go for something designed for the job like a secondhand Trend/Elu overhead router table: 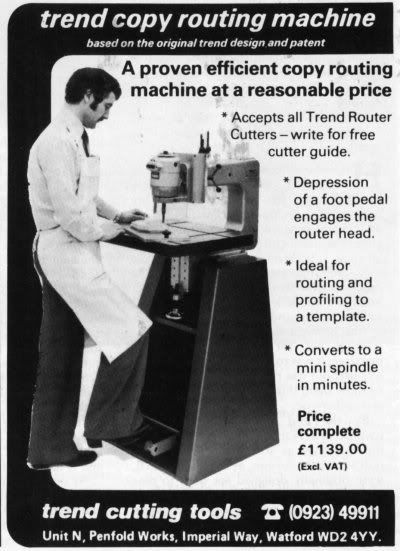 which utilised the single-speed Elu MOF11 motor still available as the deWalt DW627. The nice thing about these units is that the router motor can be used either overhead (ideal for template work) or underneath: 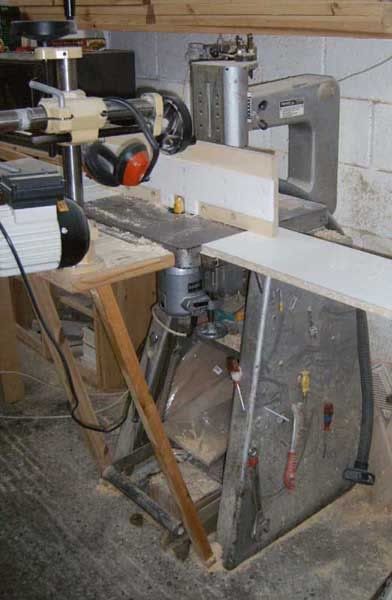 Elu certainly sold a similar stand for use with the MOF11 and the later MOF31 plunge router. Big downside is the single fixed speed of 18,000 rpm so you'll be limited on cutters you can use. Also you'll have to look for a secondhand unit as manufacture stopped in the 1980s. But the DW627/MOF11 motor is industrially rated and utterly bomb-proof (not to mention rebuildable) Lastly you could always dispense with the router for table work and move over onto the spindle - surely in the longer term a better move? I know that I'm swimming against the trend here (no pun intended!) but I feel that portable routers were never designed for long-term router table use (for one thing their motors are only rated for intermittent use) so they'll never be truly reliable in such a role. It may be that your production levels have reached the point where you need to invest in something more durable. Scrit
|
|
|
Post by jfc on Jul 27, 2008 18:46:47 GMT
I've used the cheapy tools to get me out of trouble before and i burn them out within a few weeks ...but it's fun doing it ;D I can see your point though as its stuck in a table so the quality of the tool doesnt matter really as i just need it to spin and the router table and Xtreame Xtension are where the quality is needed . The Legacy works as an over head router if i fit the linear feed table but i dont fancy having that in the middle of the workshop . I do use an extractor but the drop in hose size to get it to fit the table makes it not much use . Most of the problems have been brushes worn out and this time it'e the armature , would dust cause that  I might go for a cheapy to see how fast i can break it ;D
|
|
ivan
Junior Member

Posts: 56
|
Post by ivan on Jul 30, 2008 13:56:11 GMT
Krenov said in his book that it took him a long time to find a shaper that would do up to 16,000rpm as a sort of h/d router table - he said as a furniture maker he wanted to keep mainly to router scale operations with 1/2" bits. I wonder why smaller models don't provide this? (8 or 10 thou rpm a bit slow) Problems for belt drive? High speed balance?
|
|
|
Post by Scrit on Jul 30, 2008 23:52:20 GMT
Krenov said in his book that it took him a long time to find a shaper that would do up to 16,000rpm as a sort of h/d router table - he said as a furniture maker he wanted to keep mainly to router scale operations with 1/2" bits. I wonder why smaller models don't provide this? (8 or 10 thou rpm a bit slow) Problems for belt drive? High speed balance? A couple of reasons spring to mind. Firstly machinery manufacturers did make high speed spindle moulders as early as the 1920s (they really weren't that practicable before the widespread introduction of ball bearings, around the end of WWI), but they were generally supplied with slotted arbors, or French cutter heads, so that the users could grind their own tooling from flat steel blanks:  Typically they used to run at 10,000 to 12,0000rpm, and believe me you wouldn't want to run one much faster than that! They were only capable of taking a very light cut as they used a scraping action. Router cutters were (and are) considerably more expensive to buy, required outside grinding unless you invested in a specialist grinder such as a Colton or Saturn (not all sharpeners did until carbide became the norm in the 1970s) and were normally restricted to use on an overhead or pin router, a more specialised furniture manufacture machine which started to appear in the late 1920s with the advent of high speed bearings capable of 18,000rpm and high speed induction motors, generally run via a phase changer and capable of running at 18,00rpm. This Wadkin LS is derived from a machine which first appeared in 1927 or 1928 and the design was manufactured before WWII: 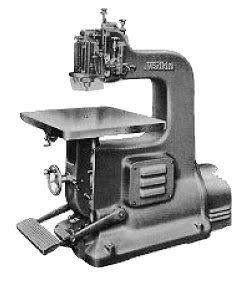 Small shop practice in the UK (and for that matter much of Europe) was more inclined towards the use of the spindle moulder with either French head or square cutter block. I once worked in a place with more than 10,000 French cutters (allegedly) stored in a huge wall cupboard with about 50-odd large shallow drawers. It took only 10 or 15 minutes to grind a new one-off profile and ticket it, hence their popularity with furniture makers until they were banned in the UK in 1974. One of the problems with Mr. Krenov is that he was in many ways a self-taught woodworker. Had he been trained in a shop with static equipment he'd probably never have bought an American-style small shaper at all, but instead would have doubtless become a devotee of the French cutter. American-style small shapers require expensive, factory made and factory sharpened 3-wing cutters or router cutters which makes them very inflexible in comparison with any form of spindle moulder where you can grind your own cutters from blanks. These days professional furniture makers who switch to using spindle moulders invariably stick with them on the grounds that the quality of cut is very good and that the cost of knives is relatively low after you've bought a block to hold them making spindle moulders a good investment. And if we're talking about slow, the 16,000 rpm is a bit slow for many router cutters. Scrit
|
|
ivan
Junior Member

Posts: 56
|
Post by ivan on Aug 1, 2008 18:43:05 GMT
I'm beginning to get the idea. I suppose we (not just the self taught?) get seduced by the handy router, turn it upside down and get seduced even further (this is Not going where you may think) and then make it permanent becuase it's so handy. A router-blinkered position keeps the shaper away?
|
|