|
Post by gazza on Aug 19, 2008 22:46:11 GMT
Came across thisand thought id ask what you all think ?? Is it a good invention or a dangerous one ?? Not quite sure myself, I can see how it would work but I seriously doubt the safety of it (just by the look of it) I have a couple of hundred feet of 6" oak skirting and 4 "archatrive with a beveled top to run in the next week or two. To be honest i wouldnt even have thought about using the thickneser, i was thinking more along the lines of the spindle moulder. Cheers, Gazza.
|
|
|
Post by engineerone on Aug 20, 2008 0:30:51 GMT
the fence on my mafell 160 p/t is adjustable to allow for bevels, so i can kind of understand, but wonder why you would use it on a thicknesser, rather than a planer  does the fence on your planer angle??? paul 
|
|
|
Post by mrgrimsdale on Aug 20, 2008 7:10:43 GMT
Came across thisand thought id ask what you all think ?? Is it a good invention or a dangerous one ?? Not quite sure myself, I can see how it would work but I seriously doubt the safety of it (just by the look of it) I have a couple of hundred feet of 6" oak skirting and 4 "archatrive with a beveled top to run in the next week or two. To be honest i wouldnt even have thought about using the thickneser, i was thinking more along the lines of the spindle moulder. Cheers, Gazza. Looks quite a neat idea if you are doing a lot of simple bevels. I'd guess one big problem would be snipe, if the thing is not sturdy enough. Next prob would be shavings getting into the rollers. But in any case I'd probably make something up myself from wood in preference. The only problem would be getting a low friction surface. I do bevels on sash sills by band-sawing and then planing over the top, down to gauge marks. cheers Jacob
|
|
|
Post by Keith on Aug 20, 2008 7:46:59 GMT
I used a simple home made (MDF) jig like this for years. Worked well enough and I did not have any safety issues with it. It does need to be robust though as it takes a pounding. If a metal one went out of adustment while feeding it could touch the blades and that would be a different ball game.
Jacob is right, snipe is a problem and would be particularly so with such a short jig. For a low friction surface I fitted strips of low friction plastic, available from Axminster.
|
|
|
Post by gazza on Aug 20, 2008 19:56:14 GMT
Thanks for the replies, Yes Paul the fence on my planer is adjustable for bevels, but i have never really had any great success with it. Saying that i suppose i havnt really give it a proper go setting up a jig on it  Bandsaw and plane to gauge marks is ok for a few small lengths Jacob, but not for a couple of hundred feet in 10ft lengths  Keith, how much were you able to take off in a pass ? I want a simple 25-30 degree bevel which will probably be around 30mm width, so a few passes at least for each length, probably take a while. Cheers, Gazza.
|
|
|
Post by engineerone on Aug 20, 2008 20:24:19 GMT
am i being silly, ;D but surely the logic is to cut the bevel on the table saw, and then clean it up either on the planer, or with a belt sander. paul 
|
|
|
Post by gazza on Aug 20, 2008 20:39:43 GMT
am i being silly, ;D paul  No not at all Paul, I had initially intended on the table saw first then a bevel cutter in the router table, but thought this would be a good enough job to take a hit (in the pocket  )for a spindle moulder. While browsing "the bay" i came accross the planer jig and just thought id ask everyones collective views. I have never thought of using the thicknesser for bevels. Cheers, Gazza.
|
|
|
Post by engineerone on Aug 20, 2008 21:01:43 GMT
gazza what i find difficult to understand is how you are going to hold the wood accurately on the thicknesser. it would seem safer to use the planer part. paul 
|
|
|
Post by gazza on Aug 20, 2008 21:06:38 GMT
Thats what the jig i posted the link to supposedly does, holds the timber at the required angle as it passes through, taking a cut. Cheers, Gazza.
|
|
|
Post by engineerone on Aug 20, 2008 21:41:12 GMT
yes but i am wondering how you support a really long piece i have enough problems with snipe on the thicknesser as it is. paul 
|
|
|
Post by scraper on Aug 20, 2008 21:44:18 GMT
To machine a load of wide skirting with a bevel recently I made a sled that supported the full length of the piece (2.4 M) from a length of melamine faced chipboard pelmet removed from the same property.
With one full length strip fixed to hold one of the long edges of the board, and one strip fixed to 'tilt' the board to the required angle it ran through the Dewalt thicknesser really well, and did the job quickly.
The manufactured jig shown remains stationary while the wood passes through, whereas the home made one passes through with the timber.
I can't claim design rights, as I saw it first on Youtube!! ;D
|
|
|
Post by Scrit on Aug 21, 2008 6:01:25 GMT
But in any case I'd probably make something up myself from wood in preference. The only problem would be getting a low friction surface. Me too. It's easy enough to make-up a bevel bed. Hard enough slippy material - never tried MFC, MF-MDF, Tufnol or HPL Mr G? Scrit
|
|
|
Post by Scrit on Aug 21, 2008 6:02:48 GMT
Thats what the jig i posted the link to supposedly does, holds the timber at the required angle as it passes through, taking a cut. Drawing coming this evg!
|
|
|
Post by gazza on Aug 21, 2008 22:08:29 GMT
thanks Scrit, I take it you find this a reasonable method of doing bevels ??
|
|
cadas
Full Member
 
Posts: 107
|
Post by cadas on Aug 22, 2008 12:53:47 GMT
I make bevel skirtings on the spindle moulder using a variable angle block.
Simple to set up and, with the powerfeed, no problem in doing long lengths (up to 4m recently in sw). The bevel is also done in one pass therefore much quicker.
The only limitation is the 50mm width of the cutter but for wider bevels it just means two passes.
Using the thicknesser method I'm guessing that you have to do multiple passes.
|
|
|
Post by gazza on Aug 22, 2008 16:45:59 GMT
I make bevel skirtings on the spindle moulder using a variable angle block. Simple to set up and, with the powerfeed, no problem in doing long lengths (up to 4m recently in sw). The bevel is also done in one pass therefore much quicker. Using the thicknesser method I'm guessing that you have to do multiple passes. Exactly my thoughts cadas, Cheers, Gazza.
|
|
|
Post by woodworker on Aug 22, 2008 16:50:44 GMT
I've used a similar jig like some of the above posts, made from various materials. This was /is a standard practice in local machine shops especially useful for making glazing beads etc. I mainly make them nowadays from MFC.
|
|
cadas
Full Member
 
Posts: 107
|
Post by cadas on Aug 22, 2008 17:40:43 GMT
I really can't see how feeding a bit of metal under your thicknesser with an 15x25mm bit of beading on is a 'happy' thing to do.
As far as I'm aware, a thichnesser is a fairly brutal, but accurate piece of kit. The infeed rollers on a commerical machine would have your hand off, therefore feeding something than is not being pressed 100% onto the bed makes me nervous.
Isn't this going against one of Scrits golden rules about using a machine for only its' intended purpose? to me this is just like cross feeding timber on a table saw to make crown moulding.
|
|
|
Post by gazza on Aug 22, 2008 17:45:54 GMT
I really can't see how feeding a bit of metal under your thicknesser with an 15x25mm bit of beading on is a 'happy' thing to do. Isn't this going against one of Scrits golden rules about using a machine for only its' intended purpose? to me this is just like cross feeding timber on a table saw to make crown moulding.  ;D ;D Cheers, Gazza.
|
|
cadas
Full Member
 
Posts: 107
|
Post by cadas on Aug 22, 2008 19:28:51 GMT
Hey....wifes away visiting relatives for a week......I'm feeling brave,
I've even left my shoes on when I came home today......
|
|
|
Post by Scrit on Aug 24, 2008 14:24:22 GMT
am i being silly, ;D but surely the logic is to cut the bevel on the table saw, and then clean it up either on the planer, or with a belt sander. Belt sander would tend to dub the edges so you might not get a crisp bevel edge whilst cutting on a table saw sometimes becomes difficult with shallow angles (coz the crown guard can get in the way) In reality this job is probably best (i.e. safest) worked on the spindle moulder with appropriate tooling (panel raising, cill or vari-angle chamfer block) if you can, but the job can be done on a thicknesser using very light passes. The (fixed) jig for doing it is like this:   You'll have to run it at slowest feed speed and you'll need to be very careful that the piece doesn't lift or kick back (in reality a couple of pressure springs or featherboards wouldn't go amiss). As you can see I've illustrated it screwed onto a planing board, a device used to help thickness very thin pieces. I'd use MFC or MF-MDF to build it with a 2 x 1in PAR batten at the end as a stop. The images below should give you an indiction of the cutting action:  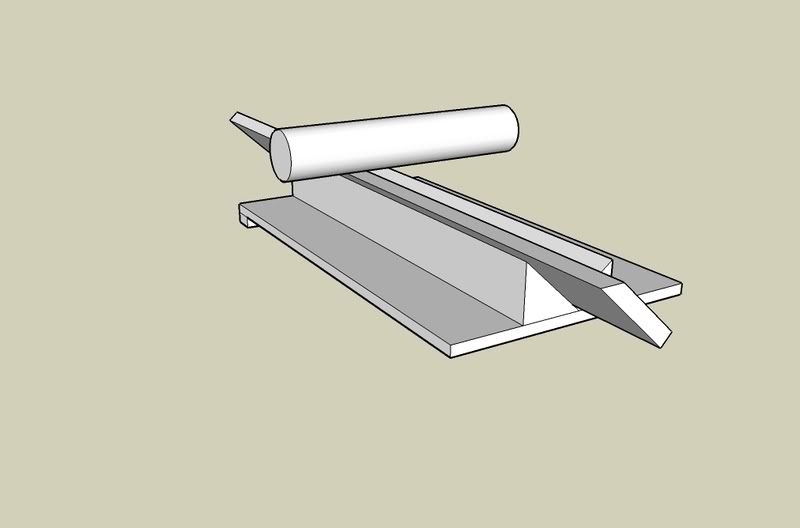 If you'd like these Sketch-Up files PM me an email and I'll send them to you. It can sometimes be easier to have a play about with a 3D drawing before building a jig I've found Scrit
|
|
|
Post by Keith on Aug 24, 2008 16:09:31 GMT
Thanks for the replies, Keith, how much were you able to take off in a pass ? I want a simple 25-30 degree bevel which will probably be around 30mm width, so a few passes at least for each length, probably take a while. Cheers, Gazza. Hi Gazza, sorry I missed this. Technically it is limited to the same amount you can normally take off in a single pass, but if you have rubber rollers, like what I do, if you try to take off too much initially the arris can cut into the rubber. I didn't run small mouldings through, if I wanted a small section I'd bevel a wider piece then cut it down on the table saw. If you try to cut too small a section the rollers may start to run on the top of edge of the jig and it doesn't do them any good; how do I know  The jig I had would only tilt to about 15 degrees, the jig was longer than the bed and extension tables so I could fit a lipping at each end to make sure it couldn't move. Now I have a spindle moulder it has gone to jig heaven.
|
|