|
Post by jfc on Mar 22, 2008 18:10:01 GMT
|
|
|
Post by jfc on Mar 22, 2008 20:41:39 GMT
While i was building this i was thinking what a great clamp up place for keeping things flat and level aswell as keeping things off the floor ..... I might deck out my whole build area like this 
|
|
|
Post by sainty on Mar 22, 2008 22:02:23 GMT
Good start JFC
A couple of questions if I may?
With the saw running on a guide is there any tendency for the saw to tip?
Presumably the saw cuts into the frame structure? Do you know how the manufactured versions cope with this? Have you made any provisions to make it "replaceable"? How do you ensure that the saw doesn't hit any fixings?
When making he cut is there a gap between the base of the saw and the material that you are cutting. Does this affect the quality of the cut? How is it affected by the depth of the material you are cutting?
Sorry to throw this at you all at once, I'm still thinking of the Shopnotes version and it will have all the same issues.
Cheers
Sainty
|
|
|
Post by jfc on Mar 22, 2008 22:31:07 GMT
A kind forum member sent me the shop notes so i know my simple version may look a bit daft but i really think it will work .
I am using the clamp and guide right now and that actually clamps onto the board . Yes the saw tips if you dont have hold of it but it runs perfectly flat with a fingertip of pressure .
The fixings are all countersunk so as long as you set the depth on the saw you wont hit them . The backing is MDF screwed to the 100 x 50 PAR so when it needs changing i can change the lot for £13 . Manufactured versions dont cope with this and you need to buy new backing . Thats why you see alot of not very old wall saws with 50 x 25 PAR fixed to the sawn up backing .
The saw is running on a zero clearance plate , i plunged the saw into the plate once i had fixed the saw to it . As i am using a clamp and guide material thickness isnt a problem as the guide clamps to the material and is not a fixed item (yet) . I need to remember material thickness when i start the next stage !
No problem , work with me on it and help debug it . It might save you 10 K ;D
|
|
|
Post by jfc on Mar 23, 2008 16:20:43 GMT
Well i got the clamp and guide mounted today and started to work out how to get it all running smoothly  Tonto gave me a hand with the next bit ;D trying to get the whole set up to stay on the frame 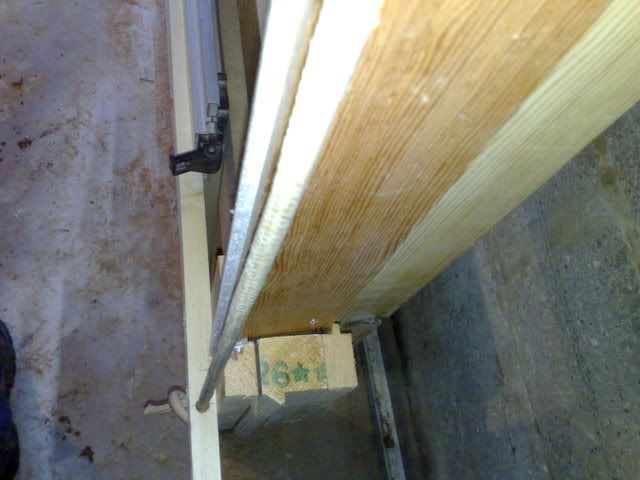  It runs quite smoothly but it can rack if you try and move it to quick . The bodge up on the end was just to see how to get it working and i think if i can find some wheels to put on the ends rather than blocks of timber it will solve the problem . Now to hunt for some wheels ....
|
|
|
Post by jfc on Mar 23, 2008 22:03:18 GMT
Ok is every one thinking i am mad ;D The frame is there and the board to run the saw on is there . I think wheels will stop it racking but these may do . 
|
|
|
Post by sainty on Mar 23, 2008 22:22:24 GMT
How about using longer out-riggers to help prevent the racking a bit? At least until you have everything running smoothly, and then upgrdade to wheels.
Rgds
Sainty
|
|
|
Post by jfc on Mar 23, 2008 22:37:18 GMT
I did think about that but as i dont need to use it right away i want to try and get it running spot on . I think wheels are the way to go , maybe three wheels clamping the 95 x 45 each end will do it . Thats three wheels each side of the 45mm both sides
|
|
|
Post by andy on Mar 23, 2008 22:42:58 GMT
Don't know if you remember the old fashioned technical drawing boards that worked on tensioned wires, pulleys and weights
May be you could come up with a similar arrangement
Still think the sliding door rails was a good idea ;D
|
|
|
Post by jfc on Mar 23, 2008 23:04:47 GMT
Thats what i am aiming for , and yes i have used them many many times . We dont just knock bits of wood together at collage you know , half the day was spent doing pretty drawings of the work we where going to do and the machinery we where going to do it with ;D
Sliding door rails are a good idea and not out of the question right now but i still think wheels will be the best option as long as they dont slip .
I'm quite happy using it as it is as it frees up space and allows me to cut full size boards but it would be nice to get it working properly so others can have a cheap wall saw that works .
|
|
|
Post by Head clansman on Mar 23, 2008 23:14:04 GMT
Hi all anybody seen the one in www.shopnotes.com at the moment i seen it a couple of days ago in one of these thread and cant find the tread now but i did download and print off it at the time i found it . I'm very interested in this as I'm shortly due to start my workshop fitting out and this look very cheap to construct and will save me a lot of space as well which will be a big bonus, but having downloaded it i cant find anywhere in the bloody description where you can buy all the metal work to go with it. Doesn't say if you have to buy individual pieces your self or if all metalwork can be bought as a kit ,any body else seen this tread. or has a copy of shopnotes.com which might say about the metal work side of the panel saw. any info on this would be very much appreciated thank in advance .
|
|
|
Post by engineerone on Mar 24, 2008 0:05:17 GMT
jason, why not use chains and gears rather than wheels to stop racking. a development of the drafting table, but i think more accurate. or even rubber belts like timing belts on cars with cogged wheels. the important thing is to be able to secure the rail in a horizontal position at each end, but then you start getting into problems with the accuracy of the stop, unless you use packing blocks under the panels you are cutting. looks good if a little basic ;D paul 
|
|
|
Post by jfc on Mar 24, 2008 0:17:01 GMT
Basic , yes . Thats the point  You dont need gears and cogs and belts to cut a straight line you just need a straight edge and a saw .
|
|
|
Post by Dave S on Mar 24, 2008 0:23:37 GMT
Would skateboard wheels fit the bill?
|
|
|
Post by jfc on Mar 24, 2008 0:30:09 GMT
Yes they would if mounted on a runner .
|
|
|
Post by Dave S on Mar 24, 2008 0:40:05 GMT
... i cant find anywhere in the bloody description where you can buy all the metal work to go with it. Doesn't say if you have to buy individual pieces your self or if all metalwork can be bought as a kit... Are you talking about the one in Shopnotes 88? Shopnotes always put info about sources at the end of the magazine. In this case, they say you can get most of what you need from general hardware stores, and for the long T track and a few other bits they suggest Rockler. They don't offer a kit of parts as such - even if they did, shipping from the US would probably be expensive. But I would think you'd find most of what you'd need from diy sheds and online. The likes of Rutlands and Axminster do T track and I'm sure someone here can recommend a good source of bearings. I've used Arc Euro Trade in the past. Dave
|
|
|
Post by Keith on Mar 24, 2008 8:54:43 GMT
|
|
|
Post by Dave S on Mar 24, 2008 10:08:32 GMT
Jason, What are you going to be using this for? Is the intention to break sheets down before dimensioning on the tablesaw, or are you hoping to be able to cut to final size on the wall saw?
I presume it would be common for you to want to rip several pieces at a time to the same width? eg when doing something like your tv unit?
I'm wondering how you are going to set the saw to cut the required width quickly and repeatedly without having to faff about resetting the saw each time.
How about extending the blocks at the end of the rail vertically upwards and put a scale on each one. You'd need to allow for the kerf but that shouldn't be hard to do. Then fix a fence between the two, running parallel to your rail. The fence would locate on the top of your sheet. Make a cut, remove the piece, move the rail down until the fence locates on the top of the board again and repeat.
I did something similar with a conventional sawboard before I bought my rail system. Come to think of it, it's much like the repeater or cabinetmaker attachment for the EZ rail that ColinCott uses.
Anyway - some ideas to toss into the pot!! ;D
Dave
|
|
|
Post by Head clansman on Mar 24, 2008 10:18:24 GMT
Hi Dave
Thanks for that, think your probably right about shipping costs , i was mulling it over in my sleep all night trying to think of ways i could get around the design in places which i think I've cracked ( need now to get it on paper ) and I've made a few improvements as well.
Thing like tee track toggles and locking knobs I'm sure i can get locally i already have Some square 50mm heavy duty aluminum tubing ( small design change there) which is long enough. I have a mate who could get the bearings , I already have the straining wires .
I'm stuck for ideas where to get the metal wheels for the straining wires and those long 16" double springs ( anybody any idea on those) would be very much appreciated. thank you in advance.
|
|
|
Post by jfc on Mar 24, 2008 11:03:35 GMT
I'm hoping to use it to cut to final size . My thinking was this ..... I have only ever used a guide rail system or bits of timber to cut boards . If i know what i need i get the timber yard to cut it but if i'm not sure what the sizes are i need to do it myself and i dont have the room in the workshop ( without shifting loads of stuff ) to lay a board out . Building the frame has solved that problem already as i can now clamp the guide to the work and cut it . The problem was clamping the guide on as you need to push the stop at one end and then clamp it at the other while holding the guide in place . Got over this problem with the sash weights . Soooo now we are at the same point as using a guide rail system in a normal way but virtically . Yes you need to use marks to get the rail in the right place but you need to do that with a rail system anyway . Doing multiple cuts can be done by setting stops to pull the rail down onto , push the rail up , add the next board and pull the rail onto the stops . This can already be done as it is . But i do like the idea of having a stop at the top to drop down onto the board . Now heres where my crazy plan comes in ;D getting the rail to run square . I think if i can set the rail square and attach two sets of tyres at each end so it grips the runner then the whole rail will move as one . Of course if it doesnt grip properly then it will rack again . I thought about Pauls chain and cog idea but i dont think it needs to go that far , but i could be totally wrong of course . Anyway ive thought about it and talked about it for to many years now so i decided just to build the thing . The frame is there and whatever i have done after that can be taken off and redone if it doesnt work .
|
|
|
Post by 9fingers on Mar 24, 2008 11:41:40 GMT
There are a number of very cheap bearing supplier on ebay. you could make wheels from a bearing and two large washers sandwiched together. Could be made from aluminium on a wood lathe with care or even a drill press with even more care. They don't have to be accurate. The springs need to be matched to the weight of your saw and carriage. instead of springs you could use sash weights or similar. Springs can be bought from RS components, LeeSpring, springmasters and possibly buck&Hickman now part of Farnell group. You will almost certainly have to buy 5 or 10 but you can alway join them together to get the length. I'd leave these till last when you can work out what performance spring you need. I found this source of useful calculators the other day www.calculatoredge.com/index.htmshould be something to help in that lot but I've not looked in detail at them. Do keep us informed with progress plus pictures naturally!! hth Bob
|
|
|
Post by Head clansman on Mar 24, 2008 12:03:45 GMT
hi bob
I will be some time before it gets made , first back to the drawing board to see if changes i have thought of can be made , in my mind it should be no problem , when that's done i 'll make my first post showing changes hopefully so other can copy.
I need to contact all companies named for parts needed, and to get a general costing , hopefully I'll be able to source all parts in this county , I'll keep you posted with pics.
|
|
|
Post by engineerone on Mar 24, 2008 12:07:32 GMT
whilst i agree jason that you are going well to producing a simple yet effective system, my fear with all these is the more you move the rail/guide system, the more errors you introduce. the advantage of a gear and weigh shaft is the solidity and hence ease of ensuring that the guide stays horizontal and square to the wood. so i have another idea which also relates to elf and safety. why not restrict the up and down movement of the rail, and move the wood itself. the idea is to have the saw and rail at say 36 inches off the ground, and allow it to move upwards by no more than 6 inches. this is then in easy hand movement and you can walk along comfortably at that height all day long. at each end of the rail up rights, you could drill holes for 1 inch dowels/pegs at say 3 inch spaces. next make up a set of horizontal planks which are 12 inches high, and have spacers between themselves and the verticals, these would be fractional and allow you to cut at any height whilst making sure the rail is truly horizontal to the proper base. i know you like all of us do not like to use maths too often once you have laid the job out, but the important thing is to remember what scrit says about the trade machines, they need re setting frequently. so if you stop the rail from moving to far, you reduce the innaccuracies there, and stop problems being caused. hope this helps  paul 
|
|
|
Post by jfc on Mar 24, 2008 12:26:40 GMT
I know what you are saying Paul but you need to move the rail out of the way to get the board on the setup in the first place , also i dont like lifting 8x4 sheets more times than i have to .
|
|
|
Post by engineerone on Mar 24, 2008 13:35:26 GMT
yes, but if you make the rail lift off and replace, it won't move. more importantly since the major reason for using a rail is to repeat cut, then one needs to keep the cutting blade at the same height to ensure repeat accuracy. hence the attachment that colin has on his ez. i agree about shifting board, you know what i feel about it  but even when one lays out a cutting plan, one inevitably ends up with needing to cut from a number of boards something of the same size, one therefore seeks to make all these cuts with the same blade set up, to ensure accuracy. and thus ends up moving a lot of boards  i know a recent task screwed that up royally by trying to get all the cuts on one board before moving to the next, and thus we ended up with 2-3mm errors  paul 
|
|