robo
Junior Member

Posts: 70
|
Post by robo on Jul 26, 2008 20:25:10 GMT
Now Lyndhurst have their web site up and running they no longer seem to be using Ebay. New price for the "gold" plated model is £995 plus delivery plus extras for the add on tables!
Perhaps an old Wadkins or Startrite would be a better choice - if only more were single phase?
R
|
|
|
Post by Scrit on Jul 27, 2008 10:05:15 GMT
According to the Ebay listing, this saw features a left tilting blade for maximum safety. I can't see how right or left tilt impacts on safety. The Lyndhurst Deft saw: 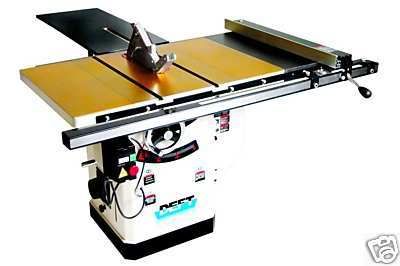 Left tilting saws are a bit of a knee-jerk reaction IMHO. If your saw has a straight-through fence such as this Startrite:  then a left tilt saw is supposedly less likely to generate kickback as a result of pinching during a bevel rip. Or at least that's the theory. The problem is that that approach doesn't take into account the effect of stress relief caused by a rip cut which can result in the timber opening outwards and jamming between the blade and the rip fence. The only effective way to deal with that is to have a rip fence plate which can be pulled back into the short position, which the Lyndhurst Deft machine already has: 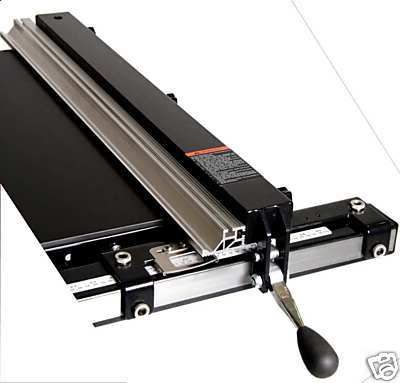 think about it mate, most saws use a right hand fence for cutting past the blade, so a left tilt would mean any angled work would have the thicker end on the bottom of the table, hence be somewhat safer. I think we'd better agree to disagree on this one Paul. You're obviously reading those bloody American books, again! (For reference try Sherlock or Stephenson) Your thinking is actually the opposite of current European practice (and all industrial table saws in the EU with the exception, I think, of one Martin machine which can tilt either way, are right tilters). The approach for bevel ripping is that the waste piece should be to the left of the (right-tilting) blade with the maximum width of flat timber against the table on the fence side (i.e. to the right) of the blade. If you need to bevel rip a very narrow strip then you're doing things wrong - bevel rips should always be taken from the edge of a piece wide enough to support itself - if it isn't wide enough then discard it or hot melt glue it to a backer piece to make it stable. The bevel cut should be a light cut and if you've followed standard practice in dimensioning your timber before setting out it will be square edged and almost the correct width already. The waste piece from this bevel rip is therefore of light section (if needs be you can even make several passes each with a deeper bevel to ensure that waste off the cut is even lighter) and it will in any case derive support from the riving knife as it exits the blade, but I agree that you do need to watch out for it getting caught on the rising teeth. In this single rare instance American practice is possibly slightly better than European (there's a rarity), although any advantage is probably more than negated by their insistance on using the straight through rip fence as opposed to the European short rip position rip fence. I also have to say that bevelling can equally well be performed on a spindle moulder, pin router, router in table or hand held router with appropriate tooling and that all of those techniques generate a much better surface finish than using a saw and that it all of these techniques is safer. On the other hand there are safety concerns over left tilting saws when the mitre or crosscut fence is used in its' conventional position to the left of the sawblade. In this case the top of the tilted blade is further over towards the mitre fence or crosscut fence, and therby closer to the operators fingers when making a bevel or compound bevel cut. Right tilters place the top of the blade further away from operators fingers when doing a crosscut. I've tended to do a lot more mitre and cross cuts on table saws than bevel rips so I know which approach I think is preferable. I will say that the Deft saw rip fence appears to be a good design in that it not only permits the use of a short position rip fence (safer) but it also seems to be of the high-low type. That means it should be possible to rip narrow strips without the need to remove the crown guard (also safer), a proceedure which requires the making of a secondary rip fence plate on rip fences such as the Biesmeyer. I doubt that the Deft saw rip fence has the rigidity of a modern Euro industrial saw, such as the Wadkin or even the Rojek, but then the price is much lower. In addition Lyndhurst have provided what appears to be an adequate run-off table with the saw - rather than worrying about right or left tilt many home woodworkers should probably be more concerned about run-off support as unsupported long work pieces are a potential kickback hazard if the lift or flex into the rising blade (and in that case it doesn't matter if your saw is a right or a left tilter). Overall, though, I think Lyndhurst should be commended for addressing so many of the design flaws to be found in almost all low-cost Chaiwanese clones of the now (very) dated Unisaw design. Scrit
|
|
|
Post by wizer on Jul 27, 2008 13:03:05 GMT
I do like this saw. Scrit: What is your opinion on this 'gold' plated top? Gimmick? Also this crown guard is not one I have seen before. Better?
|
|
|
Post by Scrit on Jul 27, 2008 13:28:39 GMT
The "gold plated" top is probably TiN (titanium nitride) - well at least they say titanium so Lyndhurst are half way there in the description. I know that TiN is used on engineering cutting tools to prolong the life of the cutting edge when the tool is new simply because it is harder than hardened high speed steel. However, it's also used on cheap woodworking drill bits where quite frankly better quality tool steel/hardening would actually be more effective in the longer term (mainly because the damned things are made from soft or poorly hardened tool steel to start with which quickly wears out once you've worn off the coating - and then they won't hold an edge because the underlying tool steel is so crap). Personally I'm struggling to see how it could give you any major advantages in a cast-iron work top. Most cast iron is reasonably durable and it normally takes 30 to 60 years industrial use of the average table saw or planer to produce any major wear patterns - so much more usage that you'd expect to see on a saw aimed at the home woodworker/very small cabinetshop market. I suspect, therefore, that the TiN is a gimmick The crown guard is a rather curious shape:  but the idea of having a "ski" or "sled-runner" shaped fore part is not unknown, as shown in this after-market Alfa crown guard sold for industrial panel saws (as a low-cost replacement) shows:  I know this is lower, but the angled lead in works in the same way as the Lyndhurst. Maybe it's just that it's an unfamiliar approach Scrit
|
|
|
Post by wizer on Jul 27, 2008 14:51:49 GMT
thanks for that Scrit. It's on my short list, along with the Jet Super Saw and the xcalibur 806
|
|
|
Post by Scrit on Jul 27, 2008 17:16:57 GMT
Now Lyndhurst have their web site up and running they no longer seem to be using Ebay. New price for the "gold" plated model is £995 plus delivery plus extras for the add on tables! yes, but that's only if you insist on having the gold one with the TiN plated top (and is it really worth paying an extra £200 for something you probably don't need?). By opting for the Silver T30 with 762mm rip you come down to a more reasonable £795 and at that they appear to throw in the rear run-off table, too. If they don't you're a woodworker, aren't you? ;D Were you to buy a secondhand Wadkin or Startrite you'd still have to arrange transport, same as you do with any large piece of kit, so fundamentally I think you've just got to live with that (and to get things into perspective moving an Altendorf panel saw is at least a £250 job wherever it goes) Perhaps an old Wadkins or Startrite would be a better choice - if only more were single phase? Dream on. At least with Startrites you are more likely to find single phase machines because they made a conscious effort to sell to sell-healed hobbyists as well as schools and the small end of the trade. Wadkin on the other hand were focused rigidly on trade sales with the odd training centre contract but generally only when the local salesman or dealer was a bit quiet as the paperworjk involved in tendering can be a nightmare. Otherwise trade generally means 3-phase. I think that £800 isn't a bad price when you consider that a mainly plastic Makita/Bosch/deWalt portable saw, like this DW model:  will end up running you circa £500 to £600 (and they're a lot smaller) whilst a half decent AGS will cost £400 to £800 before you convert it to single phase (at another £150 or so). I've worked on the Makita portable saw - nice little saw but a tad small, slightly underpowered and you do wonder how durable they are (same goes for the Bosch I took a look at). Lyndhurst seem to have addressed some of the main issues with these Chaiwanese Unisaw clones - the poor design of rip fence and lack of riving knife - so when is one of you guys going to pop over there and do us a report on how good or bad they really are?  Scrit
|
|
Stree
Junior Member

Posts: 98
|
Post by Stree on Jul 27, 2008 19:09:52 GMT
Could you give some examples of these "unisaw clones"? IE: the ones without riving knife and with poor rip fence? I do not doubt that there are some but I cannot bring to mind any recent table saw that does not have a riving knife.
|
|
|
Post by engineerone on Jul 27, 2008 19:40:56 GMT
mea culpa scrit i have been reading too ;D i take your views as you mean them, and accept the premise, i was trying to remind people that it is important to have the majority of the piece to the right of the blade to reduce problems. i agree with the overall perspective you have put on. as you know i have one of the earlier Dewalt 744 saws, and find it decent for its purpose. although, mine being earlier may well be less plastic than the later ones  the list price certainly gave that kind of impression  it works well with smallish panels, and is decent for much of the solid timber i am presently using, but my hand skills are improving. a little ;D paul 
|
|
|
Post by jake on Jul 27, 2008 20:09:13 GMT
Could you give some examples of these "unisaw clones"? IE: the ones without riving knife and with poor rip fence? I do not doubt that there are some but I cannot bring to mind any recent table saw that does not have a riving knife. Loads of them have a splitter instead of a riving knife.
|
|
|
Post by wizer on Jul 27, 2008 20:19:40 GMT
I'm planning a diversion to Lynghurst en-route to Westonbirt.
|
|
|
Post by Scrit on Jul 27, 2008 22:41:18 GMT
I'm planning a diversion to Lynghurst en-route to Westonbirt. Let us know your impressions of the machine. I'm all agog..... Scrit
|
|
mikeb
New Member
Posts: 14
|
Post by mikeb on Jul 28, 2008 7:50:44 GMT
I used to do work with a company who made HSS circular saw blades for the metal cutting industry and some of their blades were TiN coated in order to make them less likely to suffer from "pickup" - bits of swarf "welding" themselves to the sides of the blade causing the blade to "grab" in the cut on every blade revolution at the site of the pickup until it eventually jammed completely and destroyed the blade (hardened HSS steel through out and so very brittle C/W wood cutting blades)
But quite how TiN plating benefits a tablesaw top....
|
|
|
Post by engineerone on Jul 28, 2008 9:55:09 GMT
it sure looks pretty though  i guess it allows them to actually make a decent profit on the machine ;D paul 
|
|
|
Post by wizer on Jul 28, 2008 16:32:01 GMT
Cautiously entering into a sensitive area:
As we all know the 806 accepts Dado blades. The Jet and the Lyndhurst are not. What is involved with lengthening the arbor of a TS? I have heard speak of it in the past. Is it relatively simple? Is it that the 806 is also fitted with a different motor to handle the Dado?
Hope this doesn't turn into yet another Dado war. Just wondering, thinking out load etc.
|
|
cadas
Full Member
 
Posts: 107
|
Post by cadas on Jul 28, 2008 16:55:53 GMT
INCOMING !!!!!!! every one run for cover this thread has gone hostile
|
|
|
Post by engineerone on Jul 28, 2008 18:40:16 GMT
ok basic premise, extending any rotating shaft that is not supported at both ends requires the bearings to be uprated, since the bending moment changes. even though it might only be 1/2-1inch, it will make quite a difference to the way in which the shaft takes the stresses, and it also needs balancing properly. to make your own shaft, you need to ensure that you understand the shaft in the machine. hth paul 
|
|
|
Post by Scrit on Jul 28, 2008 19:59:07 GMT
As we all know the 806 accepts Dado blades. The Jet and the Lyndhurst are not. What is involved with lengthening the arbor of a TS? I have heard speak of it in the past. Is it relatively simple? Is it that the 806 is also fitted with a different motor to handle the Dado? As Paul says when you extend the shaft you bcan start to run into other problems like inadequate bearings. My understanding is that for the 806 Woodford simply supply a screw-in arbor extension and disable the motor brake (which happens to be illegal). If you don't disable the motor brake then you are running a grave risk of injury. even though it might only be 1/2-1inch, it will make quite a difference to the way in which the shaft takes the stresses, and it also needs balancing properly Not to mention locking it securely onto the existing shaft being a good idea as well. Other than that you should know my opinions on dado heads - and for that matter on knock-it-out-nailgun Norm. There are better and safer ways of producing housings and rebates (e.g. the radial arm saw) and in the case of materials such as chipboard and MDF (more common over here than the ubiquitous apple play so beloved of our American cousins) better and stronger jointing techniques, too. Scrit
|
|
|
Post by wizer on Jul 28, 2008 20:31:47 GMT
Thanks guys.
I have read all the Dado war threads and know the dangers in use.
I suspected it wouldn't be as simple as chuck in a longer arbor and off you go.
|
|