|
Post by cuttingsolutions on Jul 15, 2008 21:28:51 GMT
Nick thanks for that....always struggled to understand the concept but you put it so well.....60 mm IS marginal but still there. and has been suggested is relevant to the degree of sheer. Andy....sorry I have no idea  most of the tooling these days has disposable knives and I leave it to the experts to supply the right radius....it is VERY shallow though... Simon.. Drawing cutters  Worked closely with many manufacturers for many years and never come across that one.....as Brian suggests might just be the "scribing knife" 14x14x2... Dave
|
|
|
Post by mrgrimsdale on Jul 16, 2008 6:25:38 GMT
Just a reminder for anyone interested - if you make your own cutters for a spindle, tooling suddenly becomes very very cheap; less expensive than cutters for a tatty little router. And you get versatility and the ability to make precise replicas of almost any moulding.
cheers Jacob
|
|
|
Post by jfc on Jul 16, 2008 7:24:16 GMT
At £45 to have a pair made by a computer that scans the profile whats the point in wasting time making them . Ok add another £45 for limiters but i bet you dont grind limiters to go with your cutters  Plus the fact that no one has actually said or shown how to do it .
|
|
|
Post by mrgrimsdale on Jul 16, 2008 9:58:11 GMT
I've said how to do it loads of times , here and over there  Main advantage of DIY is perfect match and cheap. Machine copy often not quite spot on in my experience Limiters easy - just rough em out with an angle grinder. cheers Jacob
|
|
|
Post by jfc on Jul 16, 2008 11:52:42 GMT
You have said you do it but i dont recall seeing any ideas on what tooling is needed what grinder blades are needed or any technical info looking into it . If i had i would have had a go at it . All the cutters i have had made have been 100% spot on .
|
|
|
Post by mrgrimsdale on Jul 16, 2008 12:11:29 GMT
4mm HSS blanks or other steel. 6" cheapo bench grinder. 2no 1/4"wheels, one square, one half round. ditto for 1/2" wheels. Angle grinder for roughing out. File or two. That's about it.
cheers Jacob PS and wheel dressing tool in case you need to adjust the profile, as well as keeping them trim
|
|
simuk
Full Member
 
Posts: 111
|
Post by simuk on Jul 16, 2008 17:32:39 GMT
I think it is a literal translation from the German for what we call scribing cutters. Are you looking at the Felder catalogue? Brian Yes i have been looking at the Felder catalogue, this is where i saw the term. So its another name for scribes! A book i had ordered turned up yesterday ( Spindle Moulder Handbook, Eric Stephenson) isbn 978-0-85442-150-3 Definitely worth a read for anyone seeking to improve there knowledge & safety on the subject. Was reading through my Jet JWS-34 LX Spindle Moulder manual today & it says "when tenoning in most cases the 3500 rpm spindle speed is best" , but wouldn't that depend on the size of the cutter? Simon
|
|
|
Post by cuttingsolutions on Jul 16, 2008 18:01:08 GMT
Mr G
I assume your limitors are an exact mirror image of the profile but 1.5 mm lower (IIRC) otherwise the old elf safety will have your guts for garters..
and I assume that the 4mm HSS blanks "or other steel" are the new safety type with holes for securing safely in the safety cutterhead....
Of course none of the rules set out in the EN847 regs apply to small one man bands or home users.....until you come to claim on any insurances and the hospital files a report on your mangled fingers......
|
|
|
Post by cuttingsolutions on Jul 16, 2008 18:03:58 GMT
Simon Eric Stephenson is the font of all knowledge on spindle moulders and tooling and is very highly respected in the industry....
A little caution though....the EN847 regs outlawed a lot of the tooling described in his many publications.....though the practices will not have greatly changed. Dave
|
|
|
Post by mrgrimsdale on Jul 16, 2008 18:18:13 GMT
Mr G I assume your limitors are an exact mirror image of the profile but 1.5 mm lower (IIRC) otherwise the old elf safety will have your guts for garters.. and I assume that the 4mm HSS blanks "or other steel" are the new safety type with holes for securing safely in the safety cutterhead.... Of course none of the rules set out in the EN847 regs apply to small one man bands or home users.....until you come to claim on any insurances and the hospital files a report on your mangled fingers...... Well yes as you've guessed I'm not entirely obeying the rules with my old Whitehill blocks - but it would be perfectly possible to comply, and still make your own cutters. !.5 mm no prob with the limiters: having made the cutter you just mark the profile on to the limiter piece but 1.5mm back, and grind away, as accurately as you want or need. To be realistic, any amount of limiter is better than none, accuracy not essential here. cheers Jacob
|
|
|
Post by nickw on Jul 17, 2008 8:08:16 GMT
Projecting the profile onto blades which are held at an angle in the block (i.e. not on a radial plane) must cause you some headaches surely, Jacob?
|
|
|
Post by mrgrimsdale on Jul 17, 2008 8:30:25 GMT
Projecting the profile onto blades which are held at an angle in the block (i.e. not on a radial plane) must cause you some headaches surely, Jacob? No that's the clever bit (as I've explained countless times before  ). You make the cutter as if square on. It won't cut properly at an angle as you know. So what you do is deepen the hollows a touch, tweak the details, all the time offering it up to a sample of the moulding, but held at the cutting angle, until it's a perfect fit. Surprisingly easy to do. Helps if you have the block in front of you as you judge the angle by eye. I only work from samples - most of what I do is replicating period detail; matching existing stuff. cheers Jacob PS Eric Stephenson (excellent book) can make this part seem very technical - as of course the angle adjustment is different for differing amounts of projection. But as is so often the case with woodworking - hand and eye skills get you there quicker and easier ;D PPS Making your own spindle cutters is much the same as making your own hand moulding plane blades and gives you a satisfying sense of deja vu - doing something very traditional, and producing equivalent results
|
|
simuk
Full Member
 
Posts: 111
|
Post by simuk on Jul 17, 2008 9:24:33 GMT
Simon Eric Stephenson is the font of all knowledge on spindle moulders and tooling and is very highly respected in the industry.... A little caution though....the EN847 regs outlawed a lot of the tooling described in his many publications.....though the practices will not have greatly changed. Dave Thanks for the warning Dave Was reading through my Jet JWS-34 LX Spindle Moulder manual & it says "when tenoning in most cases the 3500 rpm spindle speed is best" , but wouldn't that depend on the size of the cutter? Simon
|
|
|
Post by modernist on Jul 17, 2008 13:46:54 GMT
If your feed speed was zero it would be perfectly flat. Also bear in mind that a vertical cutter also leaves scallops in a vertical plane - these are just a bit skewed. Brian I've since decided this is rubbish so please ignore it  Brian
|
|
|
Post by cuttingsolutions on Jul 17, 2008 15:20:49 GMT
Jacob I assume your machine bearings are all nicely maintained with cutters and limitors that are equally well balanced? The "old style" whithill blocks were outlawed with the EN847 regs and there really should be no reason for anyone to continue using what were admitted as dangerous tools.....next you will be telling me you use the old fashioned..... only one knife in the block  Simon Yes you are quite right about the speed/diameter. I dont know the piece you refer to but it should "suggest" the diameter of the tool recommended at the 3500 rpm. for example a cutterhead 125 mm diameter can be run from 6100-10500 rpm, whilst 140 mm @ 5400-9400; 250 mm @ 3100-5300; and 300 mm @ 2600-4400 Hope that helps. Dave
|
|
|
Post by Scrit on Jul 24, 2008 16:53:24 GMT
Was reading through my Jet JWS-34 LX Spindle Moulder manual today & it says "when tenoning in most cases the 3500 rpm spindle speed is best" , but wouldn't that depend on the size of the cutter? I'd say always run at the maximum rpm your cutter is rated at and that the spindle moulder will allow without undue vibration. I recall that Jason had problems when he was trying to run some stuff at 4,500 rpm (rough running/finish). Upping the speed to 6,000 rpm (permitted by the block) cured the problem Of course none of the rules set out in the EN847 regs apply to small one man bands or home users.....until you come to claim on any insurances and the hospital files a report on your mangled fingers...... Precisely, although our local HSE person is of the opinion that even one-man bands come under the remit of the HSE. The point about insurance is very valid, both for trade and DIY. Well yes as you've guessed I'm not entirely obeying the rules with my old Whitehill blocks - but it would be perfectly possible to comply, and still make your own cutters. You certainly aren't! The reasons why the old Whitehill blocks were banned go way further than just their lack of ability to utilise a limiter. Traditional Whitehill blocks had a single bolt to hold the cutter in place and no retaining pins (Euro safety types have a single screw, but also two pins and a wedge lock which actually tightens in the event of a bolt failure). This means that if you are remiss in tightening the cutter on a traditional Whitehill block it can work loose and be ejected (the first hazard), at which point the cutter block become unbalanced and things can get very interesting......... Ever seen a spindle moulder top piece bent over at the top from this sort of thing? Not common I admit, but it did used to happen. Modern chip limiter blocks are all but immune from this handy "feature". Secondly people tend not maintain the bolts very well on cutter blocks, and they over-tighten them, so bolt failures occur and many old Whitehill blocks suffer from the mouth opening no longer being parallel, so clamping becomes less effective. Don't get me wrong, traditional Whitehill blocks were an enormous improvement on the slotted collars, French cutters and square blocks of the day when they were introduced in the early 1930s (I think), but that was 70 odd years ago! And if you are talking about grinding your own, then surely it should be possible to hand grind a cutter and limiter for a Euro-safety block in the same way - the only downside is that the time taken to grind (in effect) 4 cutters by hand makes using a grinding service very tempting Scrit
|
|
|
Post by Scrit on Jul 27, 2008 11:31:26 GMT
As a little aside to the above thread I came across this in an early 1950s book on wood machining yesterday evening:
"The modern spindle moulder of improved design, handier adjustments and higher speeds, is much safer than machines of twenty years ago.
Higher speeds are safer. At 8,000 rpm it cuts, whereas at 3,000 rpm it snatches"
Many pre-war (WWII) spindle moulders derived from designs which were originally driven by line shafting and flat belts and these were prone to sometimes massive slippage at higher speeds, especially under varying load (as you sometimes have with spindle moulders). Following WWI (in the period 1918 to 1925) we saw tremendous improvements in the quality and availability of ball bearings which quickly replaced the once-common white-metal (Babbitt) and phosphor bronze plain bearings (and allowed higher speeds). The introduction of integrated electric motors also allowed for the use of higher spindle speeds although it took industry a few years to work this out (initially integrated electric motors seem to have been merely a way to reduce with the costs associated with installing and maintaining line shaft drive systems). The realisation that integrated electric motors were able to drive machines smoother at higher speeds seems to have taken a while - for example many planer manufacturers were still offering direct drive (3,000 rpm) planers until the early 1950s - but research done in the 1930s pointed to an "ideal" peripheral or surface tool speed for machining timbers of between 1,500 m/min or 5,000 ft/min (the speed about which many modern planers run at) and 3,000 m/min or 9,500 ft/min (regarded by some as the optimum for saw blades) .
For a 100mm (4in) cutter set this would give a speed range of circa 4,800 to 12,700 rpm whilst the same figures for a 125mm (5in) set are circa 3,900 to 10,000 rpm. So it's hardly surprising that many industrial machines built in the 1950s came with spindle speeds of 4,500 and 7,000 rpm.
I'd re-iterate that running at the maximum speed allowable by the balance of the tool (as stamped on the cutter body) will always result in the best finish. Bear in mind that the tool set diameters given above are over the cutters (i.e. they include cutter projection), so a 100mm diameter cutter set will probably be something like an 80mm cutter body plus cutters and a 125mm set will be a 100mm block with cutter projections.
Scrit
|
|
simuk
Full Member
 
Posts: 111
|
Post by simuk on Jul 28, 2008 20:10:45 GMT
Hey Scrit,
Thanks mate that was an interesting read, as well as being help full. So whats a line shafting and flat belts moulder look like?
Simon
|
|
|
Post by gazza on Jul 31, 2008 17:57:42 GMT
Hi Simon, Dont know wether you have just got it or have had it a while, Have you used the jet machine yet ?? If so what is it like ?? There is a few half price on Ebay at the moment. They seem good value Cheers, Gazza.
|
|
|
Post by Scrit on Jul 31, 2008 18:27:23 GMT
So whats a line shafting and flat belts moulder look like? The nearest you'll see these days would be the old Wadkin EQ design but with a pulley in place of the motor. The "real McCoy" is actually this: 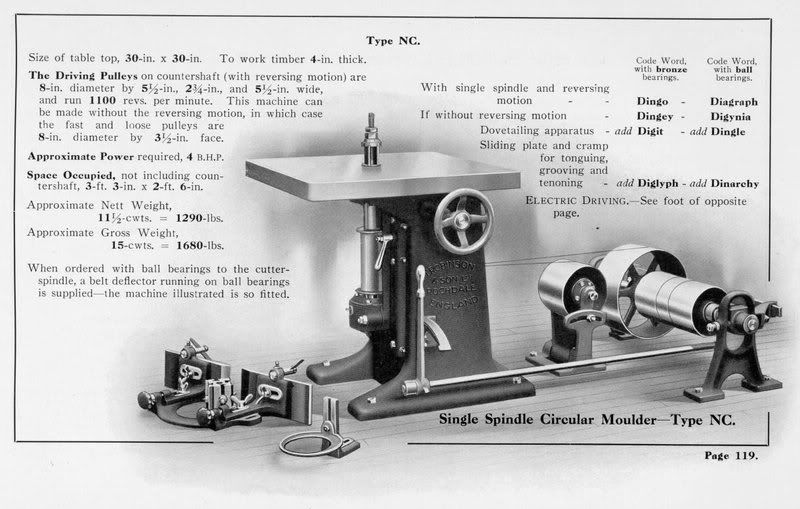 a Robinsin NC spindle moulder of the 1920s complete with the full fast and loose gear set. Not that different from a modern day spindle moulder in many ways other than the poorer bearings and lesser guards. The "fast and loose" pulleys at the back are arranged so that one has a fixed drive to the large drive pulley whilst the other one spins free. To go from undriven the lever at the side of the machine is operated and a selector fork simply moves the running belt from side to side thus going from undriven to driven and vice versa. When you knock the belt across there's a few seconds of slip as the belt is loose and acts as a natural clutch. You need to use ground rosin from time to time to keep the belts tacky so they won't slip too much. I've not used them on woodworking machines but I have used them on power looms (as I've also got other "cast-iron" interests - and no I don't wear a flat cap like Fred Dibnah before you ask) Scrit
|
|
|
Post by brackleylad on Aug 4, 2008 19:47:31 GMT
Hello guys ive just bought a cheap spindle moulder and would like your expertees on what sort of tooling to buy first. I would like to do rebating and make some kitchen doors i would really appreciate your experienced opinion many thanks
|
|
|
Post by jfc on Aug 4, 2008 20:11:08 GMT
Hi Brackley lad , and welcome . What spindle have you bought and what HP is it ? Door making blocks sets for a spindle are quite pricey ( £500 - £700 but you can buy a block and cutters to do the job for a lot less ( under £150 )
|
|
|
Post by mrgrimsdale on Aug 4, 2008 20:12:31 GMT
Depends what you want to do of course. For me it'd be 3 items: rebate block, wobble-saw unit for slots, and moulding block to hold moulding cutters.
cheers Jacob
|
|
simuk
Full Member
 
Posts: 111
|
Post by simuk on Aug 4, 2008 21:25:04 GMT
Hi Simon, Dont know wether you have just got it or have had it a while, Have you used the jet machine yet ?? If so what is it like ?? There is a few half price on Ebay at the moment. They seem good value Cheers, Gazza. Hey Gazza, Had the machine for a couple of years now, came to me second hand. Cannot really say if its a good spindle moulder or not as haven't used anything else around the same money to compare it with. What i can say is, for what i have paid for it, its earn its money, and everything i have tried rebates, grooving, tenoning , it hasn't let me down. If i had to pick some negative points, they would be, the operation instructions are terrible hardly & any pictures, and not really clear enough instructions, when you consider how dangerous these machines can be when used incorrectly, its a piss take. The access door you use to access the belt is too small. The shaper guard rattles excessively. The electrical leads that come with the machine are not long enough. If you are gonna get one, try & get the Tenoning unit with it, i couldn't really do with out it. Also if you going the second hand way try & get as much tooling chucked in on the deal as you can, chances are if there selling moulder then they might have tooling for sell aswell. Scrit thanks for posting picture, do any these get saved for museums? Simon
|
|