|
Post by engineerone on Sept 18, 2008 20:01:48 GMT
trying to learn more i thought i would try a different kind of m/t, ie dovetailed. in this case it is a cross rail on a table, i am at this time, just trying it out, and hoping to learn the best way the pin is 40 mm high and 30 mm deep, so obviously is the socket, which goes from the top of the piece down . so the question is how do you do it by hand. i have a rat as you know and may well move on to that, but would like to learn the proper way to do it by hand. i part cut with the saw, and then chiselled out the balance. so my thoughts are drill out the waste, wack it out like an ordinary mortice, or what??  bright proper  ideas please, allowing for the fact that i am using oak, in this case which is 100 x 40 wide and 600 long. paul 
|
|
|
Post by mrgrimsdale on Sept 18, 2008 20:36:06 GMT
You might have to tell us what you mean Paul. Page number in Aunty Joyce perhaps?
cheers Jacob
|
|
|
Post by engineerone on Sept 18, 2008 21:02:02 GMT
blimey jacobi thought you were the font of all knowledge ;D simple question surely, how do you cut the stopped socket on a of long dovetail? paul 
|
|
|
Post by jfc on Sept 18, 2008 21:29:32 GMT
With a dovetail cutter in a router  What that has to do with M&Ts is beyond me .
|
|
|
Post by mrgrimsdale on Sept 18, 2008 21:40:49 GMT
blimey jacobi thought you were the font of all knowledge ;D Nah not me squire - there's probably at least several things I don't know ;D ;DWos wrong with the ordinary way - mark up socket (with expensive dovetail knife, or cheapo penknife) from the tail, and whack away with a chisel. cheers Jacob
|
|
|
Post by engineerone on Sept 18, 2008 21:41:39 GMT
well i was trying to make a relationship  since you normally wack out a mortice, i thought it would be a good analogy for the socket of the dovetail, since it is made in a similar way.  paul 
|
|
|
Post by mrgrimsdale on Sept 18, 2008 21:46:43 GMT
well i was trying to make a relationship  Touched - but mrs G doesn't like that sort of thingWell yes sort of. Problem is you are doing it into end-grain so it's not like a box corner. Just have to be a bit more careful. cheers Jacob
|
|
|
Post by andy king on Sept 18, 2008 22:28:11 GMT
OK, you cut your dovetail and that becomes the template for the socket. (you can cut the socket then mark the tail, but I find tail to mark pin or socket easier and more accurate) You should have two distinct lines to saw to, one the depth of cut to correspond with the tail board, the other to give the half lap/blind back of the socket. Saw down on an angle until the saw kisses both registration marks. If these are marks are knifed or gauged it gives a positive registration for the chisel for the chopping stage. On big single sockets it can be easier to drill out some of the waste, ideally with a flat bottomed bit such as a forstner. It down to chisel work now, ideally a bevel edged chisel with very shallow bevel lands to get fully into a corners on the end grain chops at the floor of the socket, and a widish one for paring to the saw and gauge marks. Skewed chisels are handy if you have them, but you can manage with square ended ones. I usually get the socket over the leg of the bench to deaden blows and transfer the impact to full effect on the end grain chopping. Like a mortice, small close chops work best, breaking up the bulk of the waste leaving the rest for some careful paring to define the socket. Well, that's how we do it down here anyway...
|
|
|
Post by engineerone on Sept 18, 2008 22:52:15 GMT
thanks to you all, in fact i have done it as andy suggests, but was hoping there might be an easier way  back to the chisel for the test, then i may well use the rat ;D but at least i know. so is that how people do it when making the sliding dovetails on a table with a triangular base?? which i guess is the nearest to what i am trying to achieve. paul 
|
|
|
Post by mrgrimsdale on Sept 19, 2008 7:21:15 GMT
Thats how I'd do it down here too. More or less. I wouldn't use a drill though. Sounds a good idea but difficult to do neatly and the chisel work gets more difficult and fiddly.
Whats the sliding bit? Is it knock-down furniture or something? Do you mean a 3 legged table?
cheers Jacob
|
|
|
Post by andy king on Sept 19, 2008 8:09:48 GMT
Drilling out ain't fiddly or and doesn't need to be done neatly. Principle is if you have a 25mm wide socket at it's narrowest point for instance, is to use a 20mm diameter drill to remove the bulk of the waste so you don't have to chop unecessarily, (best done in a pillar drill with a forstner) leaving a couple of mil either side for paring away. Common practice.
|
|
|
Post by mrgrimsdale on Sept 19, 2008 8:17:02 GMT
Drilling out ain't fiddly or and doesn't need to be done neatly. Principle is if you have a 25mm wide socket at it's narrowest point for instance, is to use a 20mm diameter drill to remove the bulk of the waste so you don't have to chop unecessarily, (best done in a pillar drill with a forstner) leaving a couple of mil either side for paring away. Common practice. Well yes if you've got a pillar drill, or better still a morticer. I was thinking of a novice with a hand held drill or a brace and bit - difficult, easily goes off the line, or too far. But if it's smallish (furniture) size I'd rather do the whole thing with a chisel. cheers Jacob
|
|
|
Post by engineerone on Sept 19, 2008 9:07:32 GMT
if you PUSH the pin into the socket then that's the sliding bit paul 
|
|
|
Post by andy king on Sept 19, 2008 9:20:36 GMT
Still shouldn't be a problem if done with a bit of care, clamp the work down and work well within the marking out lines and you'll avoid problems. I mentioned forstners because they are flat bottomed, only a small point protruding. A worm pulled auger can easily pull through the back if you aren't careful and removes little waste when you allow for this. Mind you, don't know many pro's let alone novices who actually use let alone own a brace and bit nowadays!
|
|
dunbarhamlin
Full Member
 
Lutherie with Luddite Tendancies
Posts: 244
|
Post by dunbarhamlin on Sept 19, 2008 10:17:14 GMT
As a hamateur, I find they really ring my Stanley Bell, and if it's boring we're talking, just have to brace, myself, and put the bit between my jaws. I know, I'm all torque and no hammer action.
(Yes, I do have a pillar drill. No, it doesn't have a plug. Yes, it does work. Yes, my heating bills are quite low.)
Steve
|
|
|
Post by jfc on Sept 19, 2008 10:35:47 GMT
Only those of us that had to buy one to do the advanced craft skills test . My boss wouldnt lend me his so i had to spend a weeks wages on that and an expanding bit  Never used them since .
|
|
|
Post by tusses on Sept 19, 2008 10:44:06 GMT
As a hamateur, I find they really ring my Stanley Bell, and if it's boring we're talking, just have to brace, myself, and put the bit between my jaws. I know, I'm all torque and no hammer action. (Yes, I do have a pillar drill. No, it doesn't have a plug. Yes, it does work. Yes, my heating bills are quite low.) Steve I tried making one with a saw, but I soon found I couldn't cope 
|
|
|
Post by andy king on Sept 19, 2008 11:17:05 GMT
Yes indeed, it was needed for that part of the exams, although me being a bit older than you Jason, had to own a set of augers for day to day work, so had to buy a brace and bits to be able to work. Don't miss drilling out locks by hand any more! Wide land augers and a battery drill are certainly a lifesaver nowadays! ;D Braces can be handy for getting waste out if you are doing morticing without dedicated mortice chisels though...
|
|
|
Post by mrgrimsdale on Sept 20, 2008 14:18:15 GMT
if you PUSH the pin into the socket then that's the sliding bit paul  Sorry no wiser. So what would be a non sliding dovetail? cheers Jacob
|
|
|
Post by modernist on Sept 20, 2008 21:39:45 GMT
It doesn't pay to go away for a few days here does it  A six star rodmeister no less and further exaltation to boot ;D I think all joints slide, until they are home, then that's it! just some slide further than others. Must admit to being confused by the language. How would you class a JK wide bridle? assuming you could bear to address the topic? - a sliding M & T? Care to expand on that - I've always found it a bit of a thrutch, to borrow some climbing language. Cheers Brian
|
|
|
Post by andy king on Sept 20, 2008 23:36:45 GMT
Yep, no problem. What i was referring to is cleaning out the socket on a half lap/half blind dovetail. The acute angles make it tricky to get a square ended chisel fully into the corners to pare them out cleanly, but a skewed blade gets in there easily. A pair are handy, but you can make do with one, using the flat back on one side of the socket, and running it on the bevel on the other side. An old chisel or two can be reground to make your own if you don't want to buy specialist ones.
Andy
|
|
|
Post by engineerone on Sept 20, 2008 23:49:05 GMT
well i finally finished the first test joint yesterday late. hacking by hand, even when doing a bit of wacking with the mallet was b hard work  finally finished it off by using my home made skewed chisls i use 6mm one of each hand. makes it so much easier to get into the far corners. so if you dovetail a shelf into the sides of say a book case, it is called a sliding dovetail, making one fit a table leg seems to me to be the same. that for a drawer basically does not have a hidden socket.  paul 
|
|
|
Post by mrgrimsdale on Sept 21, 2008 8:34:35 GMT
In Joyce (p178) and all (?) the old books that'd be a 'dovetailed housing'. There's also a 'slot' or 'slip' dovetail (Joyce p 200) which is on the way to being a dovetailed housing. 'Sliding' dovetail seems to be a new term which does crop up if you google it. It doesn't tell you anything abt the joint so it's redundant IMHO.
JK's bridle joint is a feeble weak joint which is nevertheless quite difficult to do neatly. Easy to do badly. A normal M&T hides all the mistakes! It's this joint which made me think that old Jim actually knew f.a. abt trad woodwork when he wrote the books.
I still wouldn't advise anyone to remove waste from a joint with a drill. Yes to a morticer, yes to hand chisels only, but drilling out is messy and doesn't achieve much. If you don't have mortice chisels firmers are OK for mortices. Just that you aren't going to be able to hit them so hard - they'd be a b**ger to pull out and they might bend/break.
Brace and bit a useful bit of kit if you have it, but yes you don't need it if you have power tools nowadays. I still use one for yale locks. Just bought another on ebay, with an expanding bit. Never having had one before, wanted to see if they are any good. Works better than I would have thought but I imagine if you cut many 3" dia holes it'd break eventually. But could be a handy stand-by.
cheers Jacob
|
|
|
Post by thejhw on Sept 21, 2008 10:32:04 GMT
|
|
|
Post by engineerone on Sept 21, 2008 13:06:49 GMT
so this is what i have finally achieved, but since it is the first joint of this size i have done entirely by hand so although it is a little loose, it does actually assemble into a right angled and relatively close joint 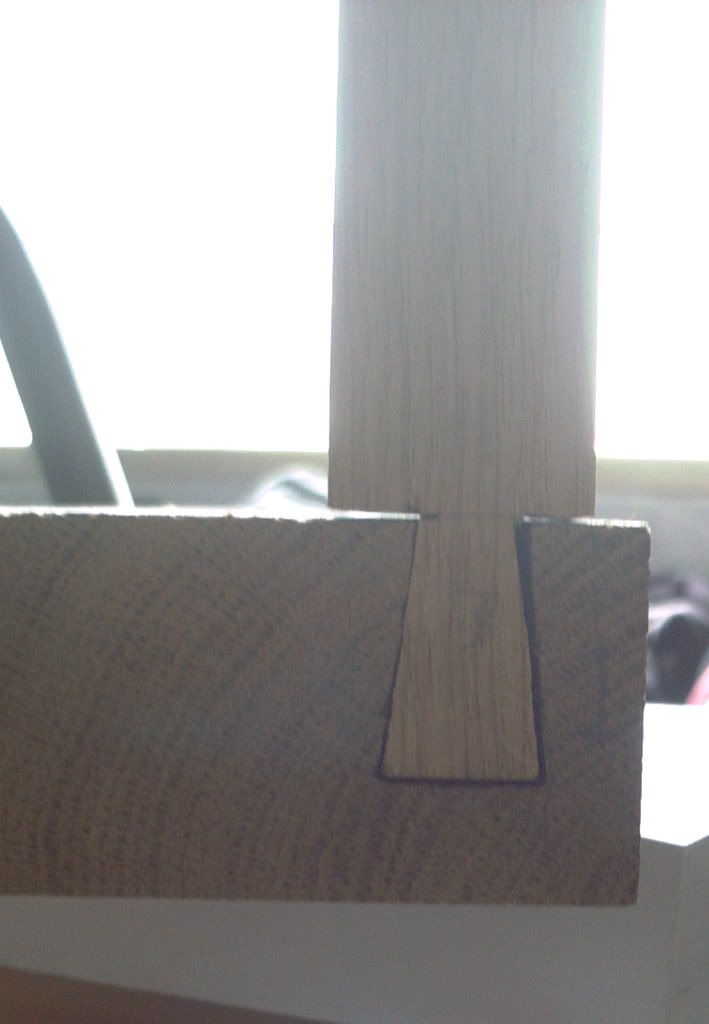 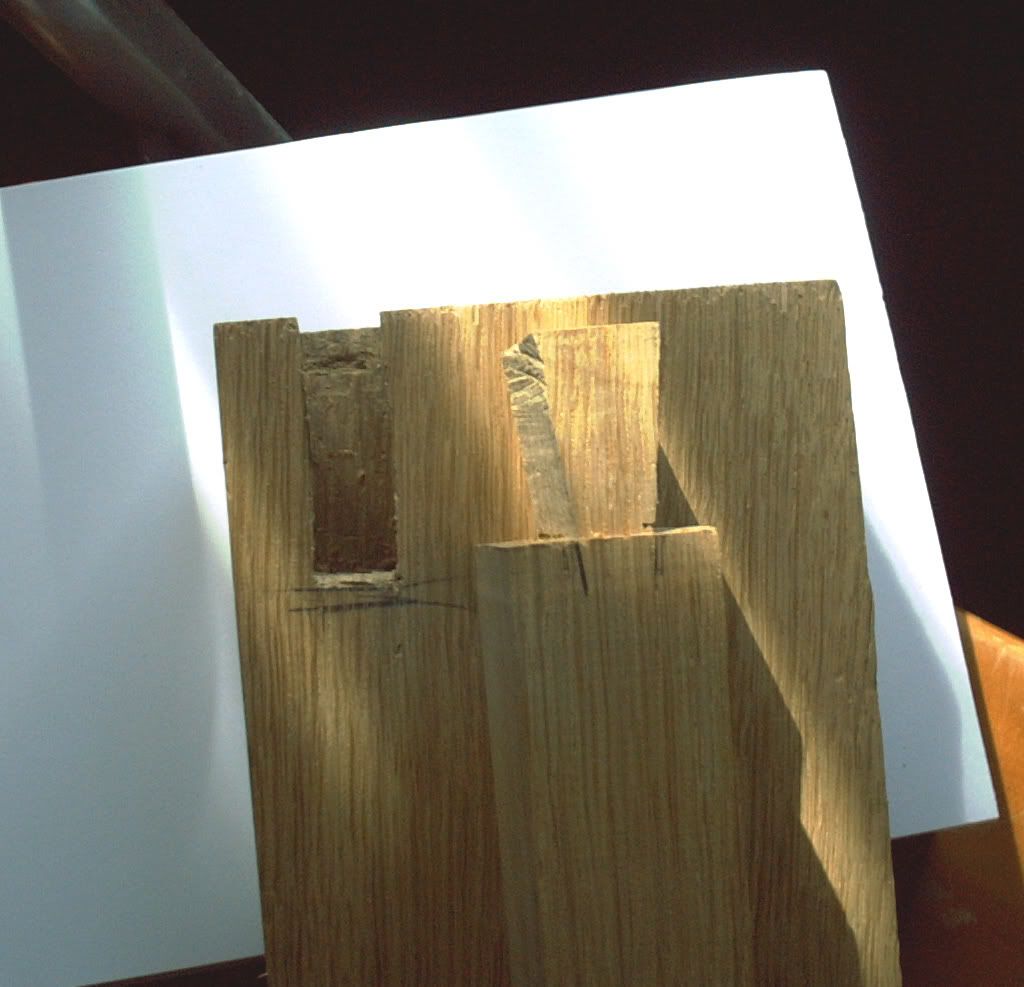 what the assembly shows clearly is that i must practice more with my hand sawing, or learn how to do it  as for the socket, actually the most difficult thing for me is to ensure that the sides are square and vertical. that is also a sawing problem i guess. ;D paul 
|
|