|
Post by tusses on Jun 22, 2008 21:13:14 GMT
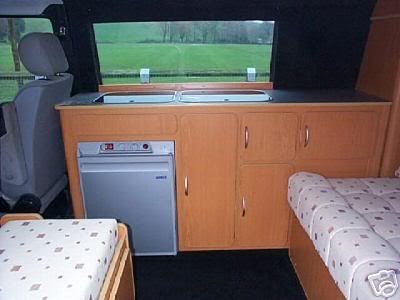 so - this kitchen unit , the front is made from one sheet. what methods are there for cutting a cupboard door into a sheet of MFC / veneered MDF etc etc its came up on another thread that plunging a circ saw might have it's problems. once cut out, the door and aperture are sloted and edged with a T section plastic edging trim. this obviously makes the process cheaper (one sheet) and quicker than making frames and doors. I have considered plunging a circ saw and jigsawing the corners - routing with an 1/8th cutter ? if you can get them - and I guess it would be slow. there must be a prefered way ? what is it ? and watch out for the next thread - where to get the trim / handles / edging/ table mountings .... etc 
|
|
cadas
Full Member
 
Posts: 107
|
Post by cadas on Jun 23, 2008 4:58:55 GMT
Router + jig
|
|
|
Post by tusses on Jun 23, 2008 10:53:40 GMT
which type of 1/8" bit would you recommend for 19mm sheet material ? ta Rich
|
|
|
Post by engineerone on Jun 23, 2008 11:07:56 GMT
i would think you need one of those with the cutting action both ways, rather than one style, this would give you a smoother finish top and bottom. paul 
|
|
|
Post by jfc on Jun 23, 2008 16:49:15 GMT
I dont think a 1/8 bit will work . It will snap , even a 1/2" shank one . I would bite the bullet and go for two sheets . One for the frame and one for the doors . I would still use a router and jigs but rough it all out first with a jig saw .
|
|
|
Post by tusses on Jun 23, 2008 17:25:28 GMT
I'm sure they are made like that because it can be done with 1 sheet ! If I used two sheets then I might as well use a face frame and traditional doors  I'll check how thick the edge trim is - maybe I could use a wider router bit .
|
|
|
Post by tusses on Jun 23, 2008 17:29:40 GMT
is there a way I could plunge a circular saw through for the straight bits and use a jig saw for the corners. Then I could neaten the edges with a router and pattern ?
|
|
cadas
Full Member
 
Posts: 107
|
Post by cadas on Jun 23, 2008 17:34:57 GMT
If you look at the photo, a bit of careful laying out should get everything out of one sheet.
On the photo, the doors look to be proud of the carcass, so they must be bigger. The only possible is solution is the 'u' shaped edged bead that you can buy.
Without CNC , you are not going to cut these doors out accurately enough to use the same piece for the door.
|
|
|
Post by jfc on Jun 23, 2008 17:36:21 GMT
They probably can be done like that on a CNC with industrial tooling . A hand held router on a home made jig ..... ive snapped enough router bits and messed up enough material to say to myself i wont even bother trying . If it where me i would do it out of cheaper material ( not faced) and laminate it or veneer it to get a grain match . Maybe the edging is the secret ? On my 70's boat ;D the last owner did it with thinner material and jigsawed it . He was better with a jigsaw than me but i can still see it was a jigsaw . 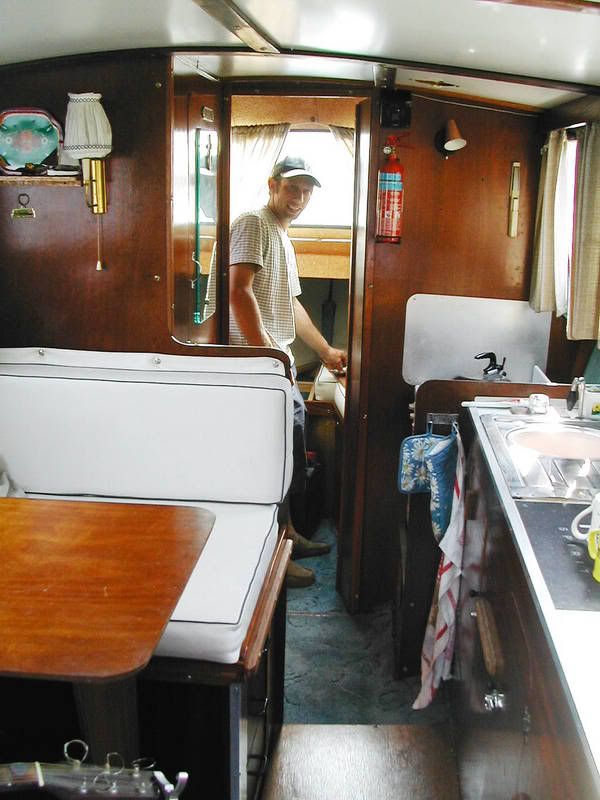 Please excuse my ugly mug in the background 
|
|
|
Post by ''The village idiot'' on Jun 23, 2008 18:00:03 GMT
I don’t know if you know you can get sheets Melamine faced chipboard and MDF 2620 x 2070 x 15 and 18mm
And don’t forget the pattern will repeat so matching the grain should not be too much of a problem.
|
|
|
Post by engineerone on Jun 23, 2008 18:42:22 GMT
i think the important thing that every body is missing is you mentioned a plastic insert.  so it is possible that you could use a 1/2 inch shank, and then when you have put the insert in , the gap to the door will not be very big at all. paul 
|
|
|
Post by ''The village idiot'' on Jun 23, 2008 18:59:21 GMT
i think the important thing that every body is missing is you mentioned a plastic insert.  so it is possible that you could use a 1/2 inch shank, and then when you have put the insert in , the gap to the door will not be very big at all. paul  Would the plastic insert be hockey stick s or even channel shaped plastic edging?
|
|
|
Post by ''The village idiot'' on Jun 23, 2008 19:00:39 GMT
I don’t know if this method will help you
On the underside of the panel mark the apertures
Rough cut the apertures to size using jig saw
On the underside of the panel temporary fix timber battens for the bearing guided router cuter to follow.
Remove all battens.
You may find that some battens can be permanently fixed.
|
|
|
Post by jfc on Jun 23, 2008 19:16:34 GMT
I have said that i have had a 1/8" cutter on a 1/2" shank snap a few times .
In your own words Paul ....There you go again , not reading posts before you reply ;D
|
|
|
Post by engineerone on Jun 23, 2008 19:19:04 GMT
you want me to read too  ;D actually jas you are right i should have said 1/2 dia cutter, whether 1/4 or 1/2 shank  paul 
|
|
|
Post by jfc on Jun 23, 2008 19:30:22 GMT
If the lipping allows for a 1/2" cutter then i would go for a 1/2" shank and still rough out with a jigsaw but to be honest it all sounds a bit sh*t . Depends what you want to do but i wouldnt go in for copying the short cuts the big boys make . I would go for bespoke and quality build .
|
|
|
Post by engineerone on Jun 23, 2008 20:39:17 GMT
i agree that it would be difficult for you to complete in price, so go for quality and try to make a decent profit. paul 
|
|
|
Post by Scrit on Jun 23, 2008 21:22:42 GMT
OK, I've had my fun prompting this so I'll now have my two pennorth. Firstly I'll say that I've designed and made PoS stands using CNC technology, but probably more significantly I was involved a few years back with a project to make bespoke camper van inserts, especially the VW and the Citroen/Talbot vans..... I'm sure they are made like that because it can be done with 1 sheet ! Without CNC , you are not going to cut these doors out accurately enough to use the same piece for the door. Even on a CNC it is simply not possible to (commercially) machine the doors out of a single piece of 18/19mm using a 3mm (1/8in) diameter bit. This is partly because the longest spirals for use on a CNC are rarely longer than 15mm and partly because they aren't particularly strong, so multiple shallow passes are required with the consequent effect on speed (and therefore cost). Paul's suggestion of an up-down (compression spirtal cut) cutter is a non starter simply because the smallest diameters ar about 9mm. Try using these 3mm cutters on a hand held router and they'll snap like twigs at the least provocation (they require care on a CNC or pin router, believe me), so I think that idea is a none starter. My experience is that the doors for this style of product are generally made separately and overlay rather than being inset. In other words they are made from two pieces and the centre cut-outs discarded. If you are using T-edging strip and insetting then the doors will need to be considerably smaller than the openings, so that might give you some leeway to use a more reasonable cutter diameter (9.5 or 10mm) but you'll still face a major problem in that PVC T-edging simply won't bend around small radii (normally minimum is radius 150mm or larger) without either wrinkling or pulling itself out of the slot over time. The insides of vehicles can get remarkable hot which may lead to swelling or drooping of the PVC so for that reason, too, I'd reconsider the approach of using T-edging (high cost is another factor). Were I you I'd also start to consider the weight of all of this. Have you worked out the surface area of material you'll require? 18mm MFC in jumbo sheets (2600 x 2100mm approx) weighs roughly 95kg - and you'll probably need 1.5 to 2 sheets per interior. That a heck of a lot of weight, the equivalent of 1-1/2 to 2 adults. If you do some research you'll find that the van/motorhome/caravan trade often uses thinner (12 to 15mm) veneer and melamine faced poplar plywood which is considerably lighter than MFC. It also outgasses a lot less. So my feeling is that before proceeding you need to do a bit more research into materials Scrit
|
|
|
Post by Dave S on Jun 23, 2008 21:52:39 GMT
On my old camper van, the doors were made as a torsion box - 1/4" veneered ply over a timber frame, edged in hardwood to match the veneer. They were certainly very light and rigid.
The carcasses were a lightweight frame skinned with ply and a solid face frame.
This was a 70's model so things have probably moved on, but I do think MFC would be too heavy.
Dave
|
|
|
Post by jfc on Jun 23, 2008 22:25:14 GMT
Same on the boat , all thin material . More room for beer that way 
|
|
|
Post by tusses on Jun 23, 2008 22:47:21 GMT
definitely chip board ! I have taken some of them apart ! at our local meet tonight I got a pic of the edge of a westfalia cupboard 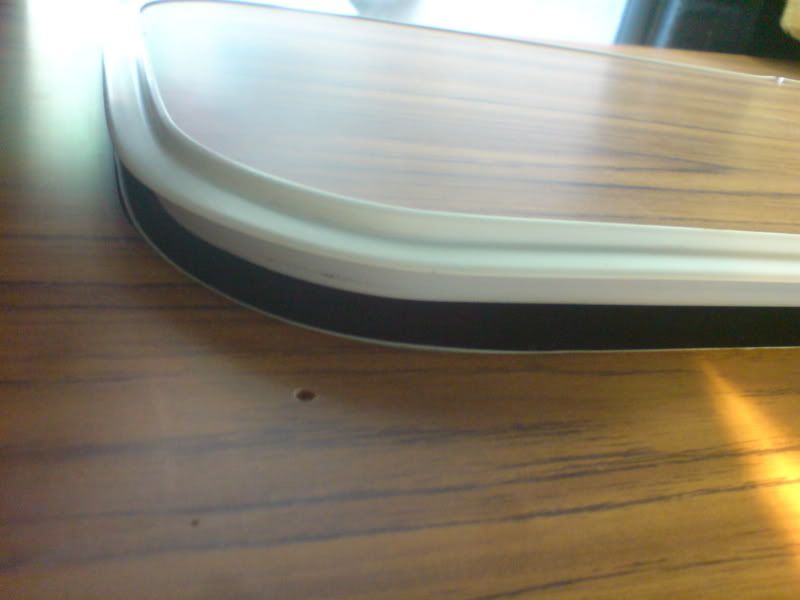 the guy has got an old cupboard in his garage he is going to let me have to copy. Its 1 peice and the edge trim makes a lip for the door to close onto. we are talking 50's to 70's vw campers - and the money is either faithful copys of how westfalia - devon - dormobile etc used to make them (each had their own layout and trims and handles etc) or it is in bespoke custom interiors - which are , as has been said, a lot easier to make ! The newer vans , again are easy as there are no 'classic' sort after designs yet. people will happily pay £1500 for a tatty - falling apart - original westy interior to put in their split screen van ! I have a 58 split and a 68 bay at the moment along with 7 T4's. the older ones really sell better if the look like the originals .
|
|
|
Post by engineerone on Jun 24, 2008 0:01:36 GMT
i do agree though that they are not made of one piece cut out. thing is it would be difficult to get the corners started paul 
|
|
|
Post by jfc on Jun 24, 2008 8:08:00 GMT
Looking at that pic i think your best bet is to get practicing with a very good jigsaw and laminate it all after . It looks to be a grain match with the door and the frame .
|
|
|
Post by tusses on Jun 24, 2008 8:50:15 GMT
ok - what kind of costs and where from for laminates ?
I guess only the outside would need to be wood look alike with the inside being white or biege for instance.
Also I could use plain ply chip mdf .... which would relive the isue of trying to cut it out of one sheet !
I've seen 'leisure ply' mentioned as being lighter than standard ply ? is this just sales shpeel ?
|
|
|
Post by lemonjeff on Jun 24, 2008 10:55:43 GMT
|
|